
The Importance of Preventative Maintenance in Emergency Response
Emergency Response organizations typically have large caches of equipment and supplies to maintain readiness for emergencies that have yet to happen. If these caches didn’t exist, then initial response would be delayed until all necessary equipment and supplies were procured. And post COVID many of you have probably experienced issues in the supply chain, which would further delay initial response. OWCN is no stranger to this concept, READINESS is one of our core principles, which includes maintaining caches of equipment and supplies.
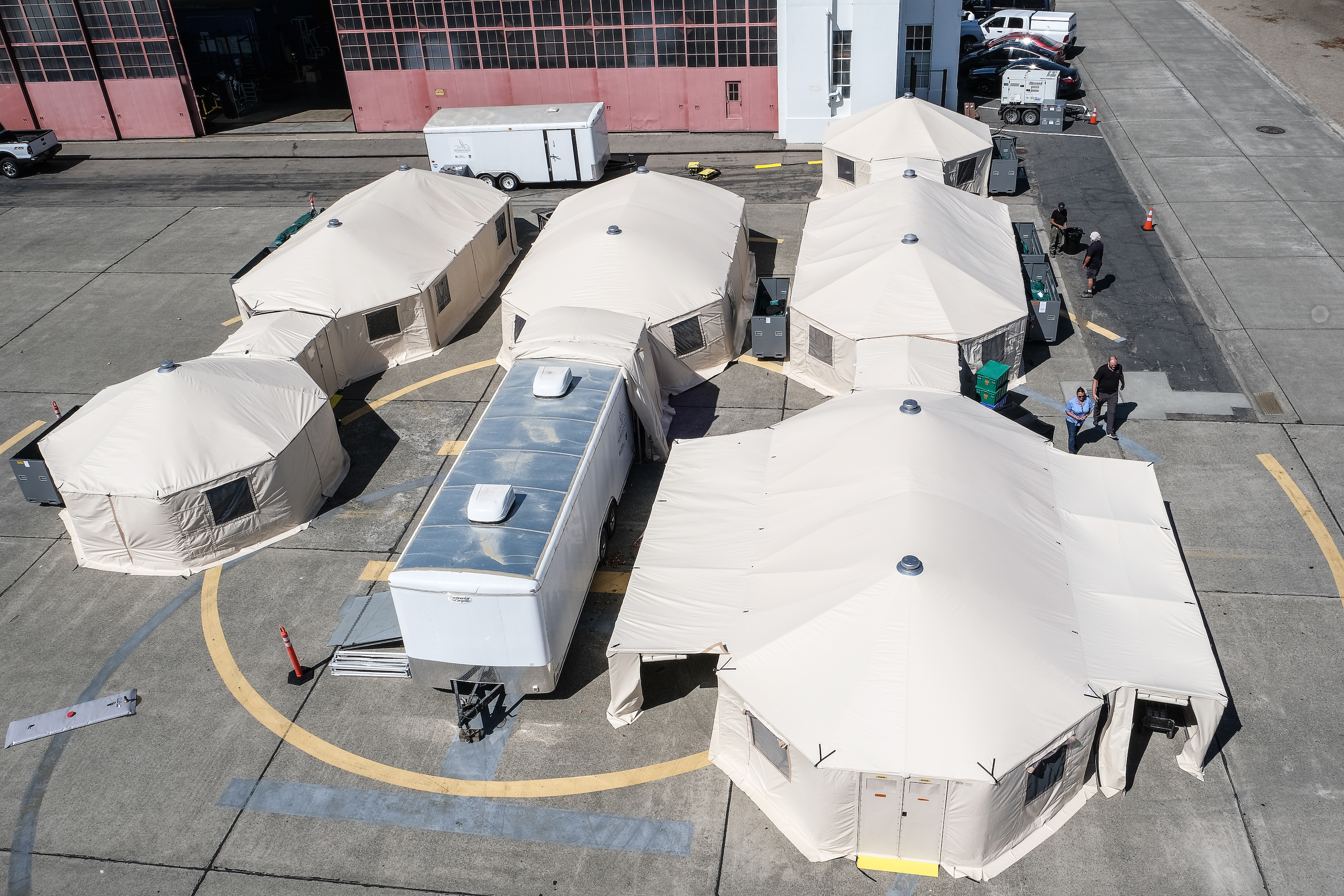
The OWCN management team maintains an extensive cache of equipment and supplies, from a fleet of vehicles to Tyvek. Each member of the management team has their “niche” or “specialty” in regard to the equipment and supplies we manage and maintain. Personally, my specialty falls in the realm of our large equipment to include vehicles, vessels, trailers, all-terrain vehicles (ATV's ), utility tool vehicles (UTV’s), and generators. Which brings me to the focus on this blog, preventative maintenance.
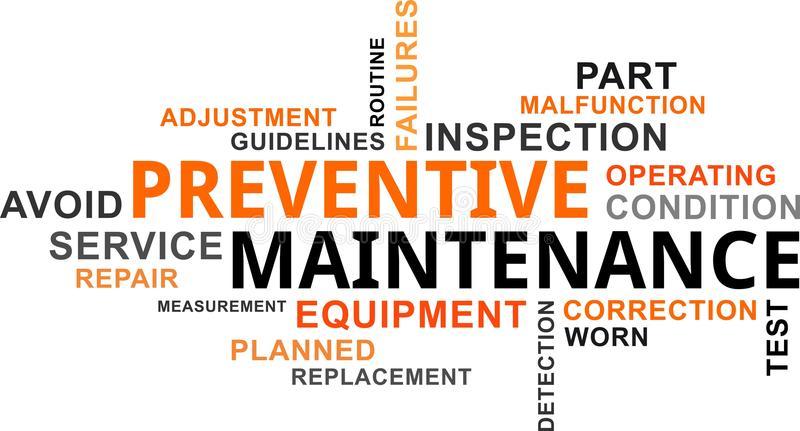
Some may think that the purchase of an equipment asset for an emergency response cache may be the end of the process. In that you have it in your inventory and its ready for deployment; not exactly. Idle equipment causes its own wear and tear overtime. Fuel kept in generators can degrade, batteries can deplete, moving parts can rust, etc. So how do you keep equipment ready for rapid deployment? The simple answer is preventative maintenance. Preventative maintenance is the act of preforming scheduled maintenance on equipment to help prevent unexpected failures. Since response equipment can sit idle for long periods, time is often its biggest enemy and to remedy this issue the OWCN logistics team has put together an intensive scheduled maintenance program for its equipment.
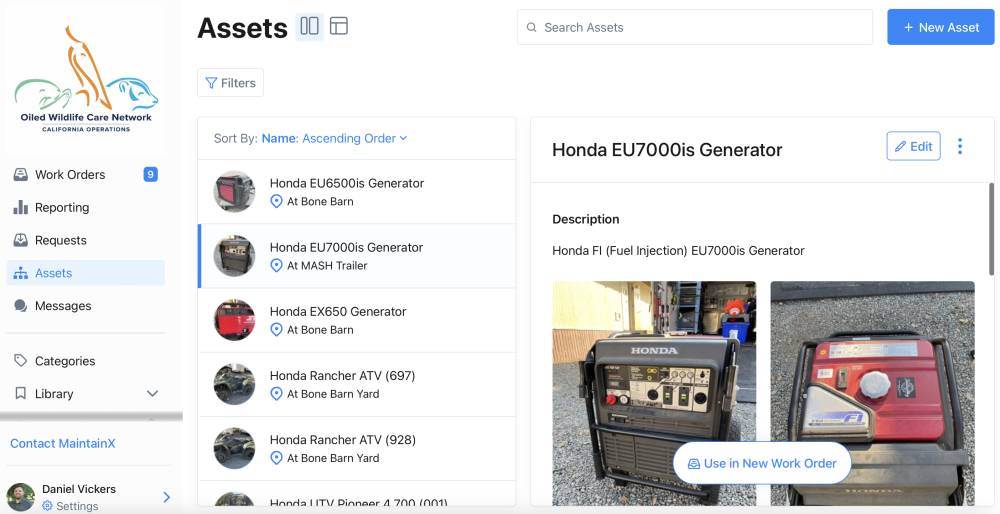
With the help of an app called “MaintainX” I can track monthly and yearly maintenance on OWCN equipment, and I can further set up workorders for any deficiencies found. Our generator inventory in MaintainX is a great example of one of our monthly preventative maintenance schedules. Each OWCN owned generator is inventoried into the app, and each is scheduled for reoccurring monthly preventative maintenance as well as a yearly. The app itself sends a push notification and email when a preventative maintenance schedule is due.
A monthly scheduled maintenance on a generator includes fluid checks, battery check (if applicable), and a functionality test to include a power generation test. Just because a generator motor is running does not necessarily mean it is generating power. A yearly scheduled maintenance includes a service to be performed by a third-party company. Just like you would for your own car for a service.
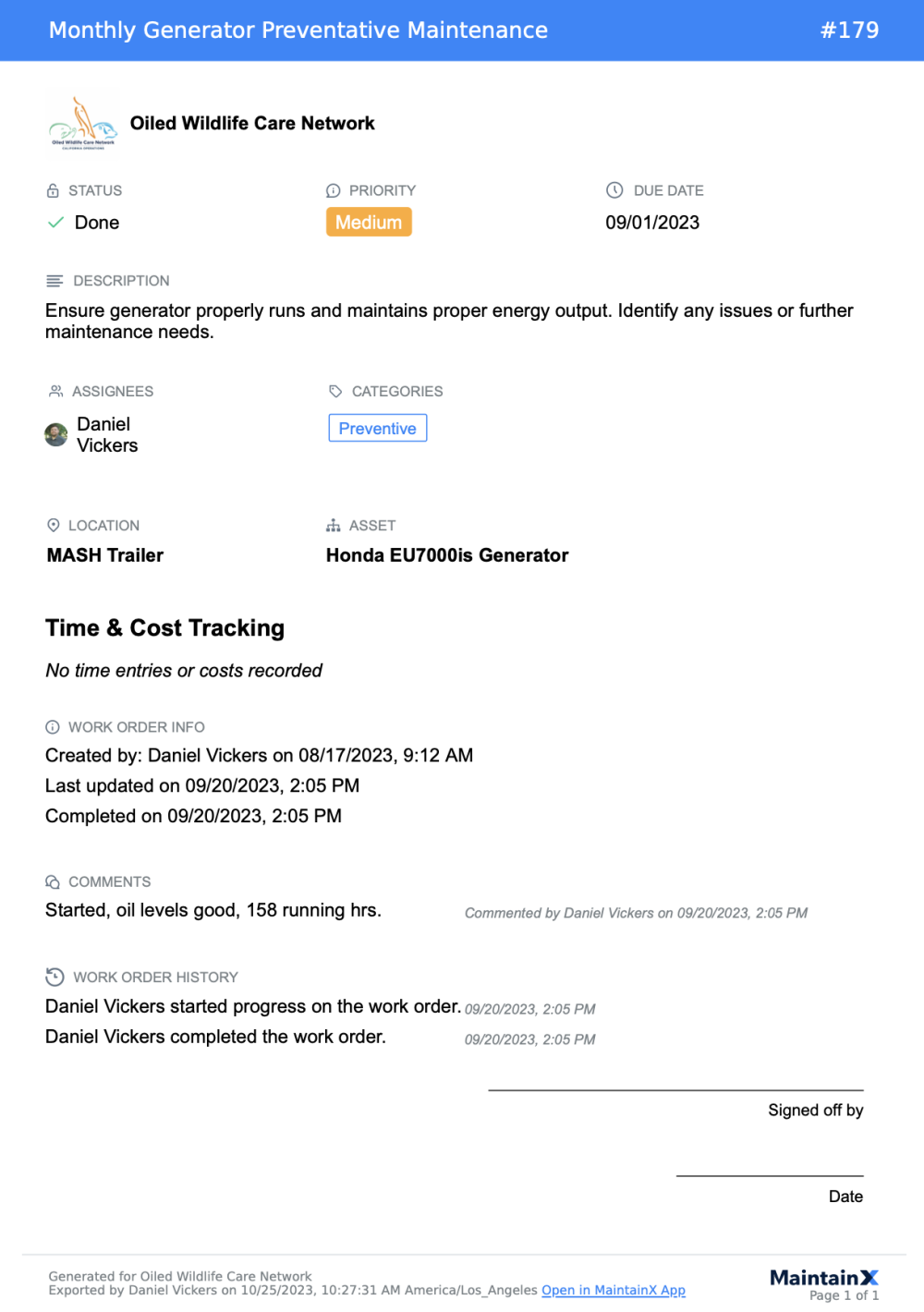
These scheduled maintenances ensure equipment will work when needed. In OWCN’s case we need to be able to respond to an oil spill without delay and to do this we need to ensure our fleet of vehicles, vessels, trailers, ATV’s, UTV’s, and generators are in good working order.
“An ounce of prevention is worth a pound of cure.”
-Benjamin Franklin
Danny Vickers
Wildlife Logistics Specialist